武汉电路设计中的可靠性过程设计
- 发布时间:2022-08-16 10:23:31
- 浏览量:632
电路设计中的可靠性过程设计
DfR中使用的结构化流程考虑了从设计流程的一端到另一端可能发生的所有类型的更改。特定数据控制着流程的各个方面。结构还包括在设计中使用工具和方法以确保可靠性的顺序。取决于项目的范围和要求,该序列可以线性发生,也可以具有彼此并行发生的一些活动。顺序也可能从一个电路或系统的设计到另一个电路或系统的设计不同。
DfR的顺序包含六个基本步骤,可帮助设计团队制定可靠的产品开发路线图。尽管DfR影响设计和开发过程的各个方面,但主要影响发生在概念和设计阶段。专注于DfR的设计团队开始在概念阶段的初期就考虑失败的可能性,并在寻找分析和提高可靠性的方法时保持这种关注。
DfR流程的合并
每个项目都应从所有利益相关者的角度出发。无论是从事航空航天应用的电路设计工作,还是将设备连接到物联网(IoT)的工业系统上的工作,设计团队都必须了解操作环境,并始终注意可能因厂商而异的期望。对需求的关注通常建立在这些期望的基础上,同时也将注意力始终放在基准,最佳实践以及对任何竞争产品或系统的分析上。
需求导致电子系统的可靠性保证
设计团队可以使用“关键到可靠性”框架来定义需求,该框架可以识别电气和机械设计如何响应物理环境和应用程序。根据不同的应用,这些要求可能会促使电路在极端温度和湿度,振动或冲击的大范围条件下持续运行。其他要求可能涉及一些限制,例如物理尺寸,灵活性或尺寸。
团队可以开发风险模型,包括对设备的历史数据,在方案设计的分析,使用最坏情况电路应力分析(WCCSA)和失效模式影响和危害性分析(FMECA)和故障率的估计值。所有这一切的唯一目的是证明电路和组件在产品的使用寿命内可以在设计规格之内或之上运行。
定量评估推动了可靠性设计。WCCSA在描述元件在极端环境或工作条件下的功能性能时,会考虑元件公差的差异。该分析包括制造商,环境,组件老化,疲劳和公差,同时显示了多种因素如何导致组件偏离规格。
设计工程师可以使用FMECA来确定潜在故障场景对电路和系统的影响。故障模式和严重性分析是通过故障树分析,建模和根本原因分析进行的。反过来,设计团队根据对成功的影响对FMECA的结果进行分类。通过应用程序确定成功的定义是仅涵盖设备,人类安全还是设备与安全的结合,FMECA的使用使团队能够:
研究设计方案
制定测试方法
建立可靠性,可维护性和安全性的基准
当设计团队完成FMECA测试时,结果将提供有关单点故障,关键故障估计,系统和子系统故障模式以及关键组件的可靠性的信息。信息树的各个部分可以指示单点故障或灾难性故障的可能性。整个信息集使团队能够确定可靠性问题区域,制定消除或最小化问题区域的计划以及可能的设计修改,其中可能包括具有更精确的公差和性能规格的新技术或组件。
FMECA的关键性分析部分按严重性和概率对失败的可能性进行排序。每个级别仅为特定应用的电路分析提供参考点。设计工程师可以使用重要性分析将重点放在重要的组件,电路,子系统或系统上,并建立故障率的近似值。概率水平通常随着电路设计的成熟而变化。
可靠性设计使设计团队走上了一条不同的道路。这条道路不仅要考虑公差,还要考虑设计公差,还要考虑影响元器件和电路的因素。结果,想到了“魔鬼在细节中”的成语。DfR不会接受模拟结果,而是会集中考虑数据,同时考虑可能导致意外问题的所有因素。
这种详细的分析使设计团队摆脱了假设,即具有Y公差百分比的组件X不管在Z电路中都能工作,并将它们指向更大的测试,分析和验证。团队可以扩展DfR流程,以不断获取有关组件和电路性能的知识,作为进行改进的一种方法。
今天关于电路设计中的可靠性过程设计就分享到这里,更多PCB相关知识, 请关注深亚电子
免责声明:部分文章信息来源于网络以及网友投稿,本网站只负责对文章进行整理、排版、编辑,意为分享交流传递信息,并不意味着赞同其观点或证实其内容的真实性,如本站文章和转稿涉及版权等问题,请作者在及时联系本站,我们会尽快和您对接处理。
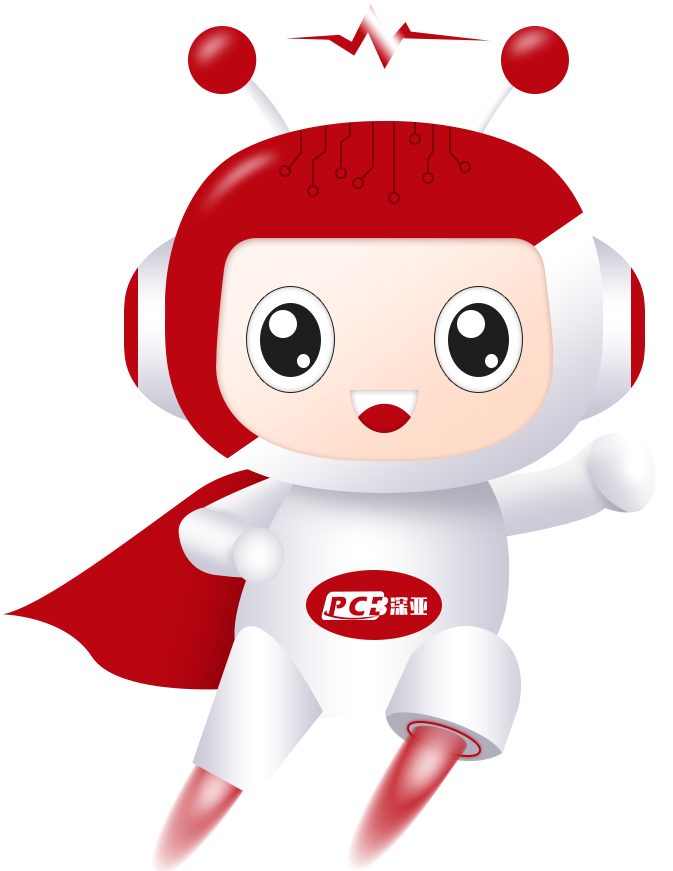